NEWSLETTER
4/2024
Advanced gas cleaning systems in the cement industry
The industry has to prepare itself for stricter requirements towards emissions reduction - evolving capture technologies are a further step in this process
The legal requirements to reduce emissions from cement plants challenge the cement industry to continuously improve its high level of environmental protection. In addition, emerging decarbonisation technologies require the adaptation or introduction of completely new technologies to clean exhaust gas streams from cement plants. Also, further emission reduction is an ongoing issue, particularly in relation to the legal framework that applies when alternative fuels/raw materials are used.
As regards airborne emissions, the operation of a cement plant must be carried out in compliance with the local legislation. Emission limits in Europe are set according to the European Industrial Emissions Directive as well as national environmental regulations. The long-time experience has shown that modern cement production is environmentally friendly and has no negative impact on the neighbourhood (figure 1). However, emissions and their respective abatement measures are in the focus of every licensing procedure, especially in light of the stricter air quality standards from 2030 on. In recent years, the cement industry worldwide has invested enormously in advanced exhaust gas purification technology. This is especially the case for nitrogen oxides (NOx) and mercury (Hg).
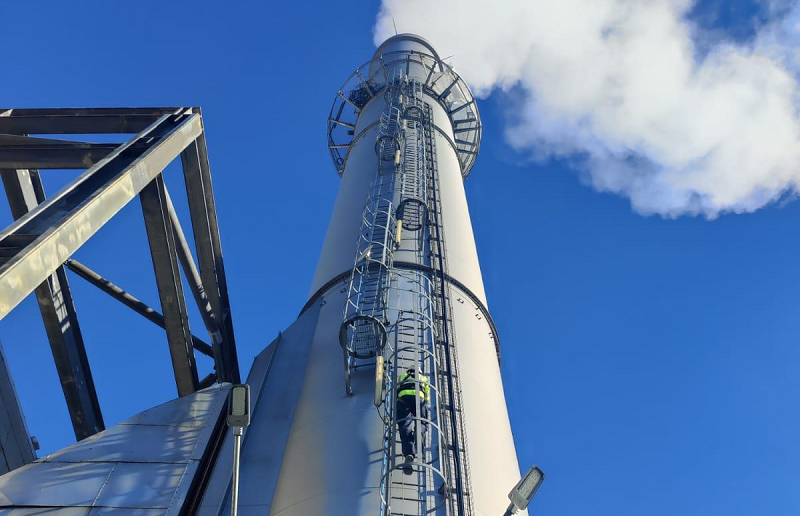
Figure 1: State-of-the-art exhaust gas cleaning systems ensure for an environmentally compatible cement production
Advanced NOₓ abatement techniques
NOₓ are produced by all high-temperature processes. For this reason and in order to comply with low emission limit values, every cement kiln line has to be equipped with state-of-the-art NOx abatement technique. In recent years there has been huge developments in the field of catalytic reduction technologies. The SCR (Selective Catalytic Reduction) process has so far been the most important catalytic process in the field of industrial flue gas cleaning. Extensive operating experience is now available from SCR projects in the cement industry. Different variants of the SCR process (high-dust, semi-dust, low-dust) have been installed in cement plants in Germany, Austria, Italy and the USA over the past 20 years. In most cases the HD (High-Dust) variant has been chosen, but there is also operational experience available with the LD variant. LD-SCR plants require higher investment costs, but as they are installed in the dedusted flue gas there is a lower risk of mechanical erosion and catalyst poisoning compared to the other variants, leading to longer service life and thus catalyst costs. Furthermore, experiences, especially from HD SCR installations, have shown that this is no “plug & play”-technology in the cement industry. Time for optimisation regarding the optimum temperature window, efficient dust cleaning, raw material impacts, poisoning etc. always has to be taken into account.
In the past years, integrated technologies have also been developed which can be seen as a combination of proven technologies for individual flue gas components. The so-called “DeCONOx” process for example is a combination of a low-dust SCR system with a regenerative thermal oxidation (RTO), which allows an efficient reduction of NOₓ, CO and TOC/VOC emissions. Furthermore, the combination with reduction of dust emissions is being evolved further, e. g. by the use of catalytic filter bags or the so called combined hot gas filtration with catalytic NOₓ abatement.
Mercury - especially in focus when using waste materials
The co-processing of waste materials in cement plants has been approved practice for many years. In this process, it is important to always ensure that the use of waste - whether raw material or fuel - does not lead to a negative impact on the environment. Permitting procedures usually focus on the emissions of mercury and trace elements, dependant on the varying trace element concentrations in different alternative fuels and raw materials. However, mercury emissions may also originate from the natural raw material. For this reason and due to the special behaviour of high-volatile components in the clinker burning process, the further reduction of mercury in the cement industry has continued to develop steadily.
In most cement plants, in order to reduce mercury emissions, dust enriched with Hg is discharged from the kiln system and added to the product in the cement mill. Additional measures can be applied, if dust shuttling is not sufficient, such as the XMercury® process, which is a relatively new technique, that aims to thermally remove the mercury from the filter dust in an additional device that is located in the pre-heater tower and operated with hot process gas. The mercury in the end is adsorbed by activated carbon or coke and separated from the gas stream in a downstream filtering separator. A first XMercury® plant was installed in an Austrian cement plant in 2015, followed by a second plant on the south of Germany in 2018.
As regards further investment in extended exhaust gas cleaning technologies, operators are faced with the fact, that - due to further CO₂ reduction - technical processes are undergoing a deep industrial transformation anyway.
Carbon capture - an „all at once“ possibility?
CO₂ is not regarded as a classical air pollutant. However, the abatement of CO₂ emissions from industry processes in order to achieve carbon neutrality will have a great impact also on the emissions of classical air pollutants. It is now widely acknowledged that the abatement of process-related CO₂ emissions will require the capturing and purification of CO₂ from the exhaust gas of the combustion process. Complex cleaning steps in an additional carbon purification unit are necessary to achieve this. Because of this, it is to be expected that the new emerging technologies for further CO₂ reduction will have to implement gas cleaning processes. On the other hand, new emission pathways, e.g. a shift to the wastewater path (due to the scrubbing) must be considered and evaluated.
This makes it all the more important to create a legal framework for fast permitting procedures, to further develop monitoring technologies and last but not least to promote public acceptance and understanding.