Newsletter
2/2023
Evolving kiln technologies - reducing fuel CO2 emissions
How hydrogen can be part of guiding clinker production towards climate neutrality
The reduction of CO2 emissions in the cement industry is a huge challenge. Even though CCU/S technologies – as a final step – will help the cement industry to reach net-zero, every ton of CO2 which is not emitted is one ton of CO2 which does not need to be captured and stored. The well-known difficulty is that the biggest source of CO2 emissions in the clinker burning process comes from the raw meal: in the preheater and/or calciner, limestone disintegrates into CaO and CO2.
The only way to lower the raw-material-based CO2 by means of conventional measures from being emitted is to optimise the clinker content in cement by means of substitution with cementitious materials. In addition, fuel-based emissions can be reduced by the substitution of fossil-based fuels, and to some degree by modernising the kiln system.
Alternative Fuels
The easiest way to reduce the demand of fossil fuels is to use more alternative fuels (AF) such as RDF (refuse-derived fuel), used tyres etc. The AF may need to be dried, which can be done using the excess heat of the clinker burning process. The availability, quality and price of the used alternative fuels as well as the potential impact on the stability of the clinker burning process itself has to be considered.
Hydrogen use
While the substitution of fossil fuels with alternative fuels is carried out by most cement plants today, the substitution of carbon-based fuels in general is possible, as has been implemented in many roadmaps such as the GCCA roadmap. Currently, research in the use of hydrogen (H2) as fuel is a major key point in the cement industry.
First tests with hydrogen as fuel in the kiln main burner were carried out under the BEIS MPA Fuel Switching Competition in the UK. In this project, a carbon net-zero fuel mix with an energy share of 40 – 50 % hydrogen was fired in an operating kiln.
A previous feasibility study concluded that the burner needed to be modified as compared to a conventional one, due to the increase in flame temperature (prevent NOx, refractory material not impinged, reduce hot spots), combined with additional hydrogen storage and pipework. However, contrary to this study, the results of the trial revealed the use of hydrogen without the need of major modifications to the burner itself.
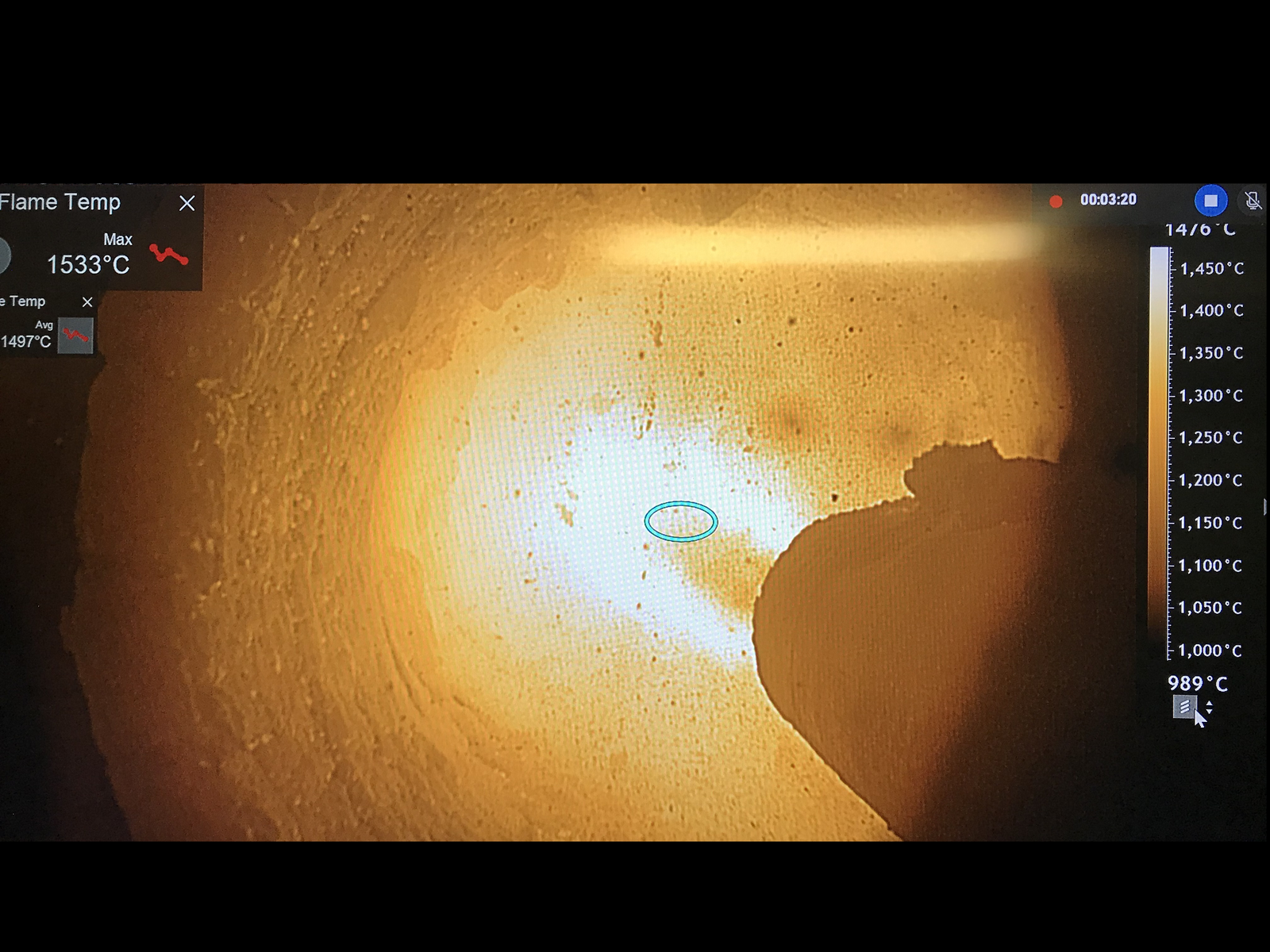
Figure 1: Flame at net-zero fuel mix
Burner characteristics
For the trial, the hydrogen pressure was reduced from the delivered ~500 bar to 1 bar. A pipe with multiple valves was installed to check for pressure losses which would indicate leakages. The valve train was connected into an armoured, flexible hose, from which it was connected to the hydrogen lance. The lance design was kept simple to be able to fit into an empty channel on the currently used kiln main burner. Hydrogen and cooling air were guided through two concentric channels. During normal operation mode, the tip velocity at the hydrogen nozzle was high enough to prevent an increase in temperature at the burner tip.
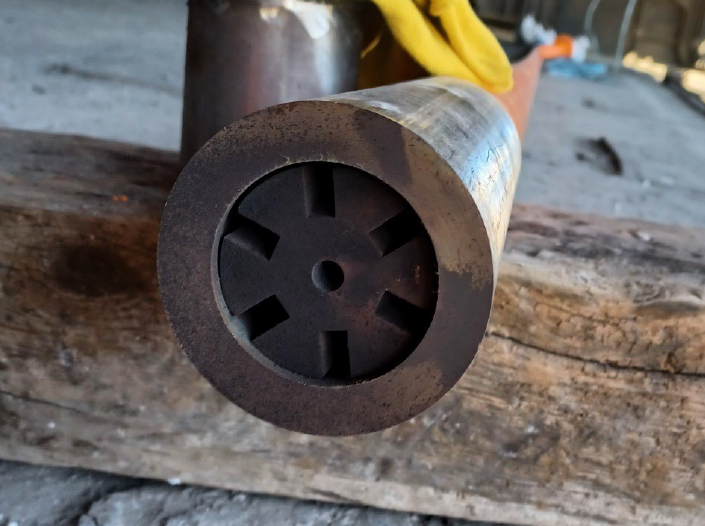
Figure 2: Nozzle of hydrogen lance outside of the kiln
The H2 lance was modified with two different nozzles for low and high flow conditions. The nozzle for low flow conditions was only used on the first day of the trial. Although both nozzles were adjustable to control the hydrogen flow, the nozzle for high flow conditions was opened to the maximum to minimise the pressure drop across the system. Instead, the flow was controlled by the flow control valve. The hydrogen gas was injected with velocities >900 m/s to keep the positioning of the flame constant. This extremely high tip velocity also prevented the burner tip from heating up.
Hydrogen is still far from being used on a broad scale in the cement sector. The availability of sufficient hydrogen at a competitive price is, from today’s perspective, the main bottleneck. However, hydrogen will have great potential in regions with sufficient carbon-free electricity once the respective capacity of electrolysers has been built up.
Oxyfuel Enrichment
Against this background the cement industry’s demand for alternative fuels will continue to increase. To further facilitate the use of AFs, oxygen-enriched combustion air can help to even utilise AFs which would otherwise require a dedicated pre-treatment. The oxygen enrichment technology – also known as Oxyfuel – increases energy efficiency, production capacity or substitution rates of lower-caloric alternative fuels. Through enrichment of oxygen, up to 5 % of the specific thermal energy demand can be reduced, which also reduces CO2-emissions by 5 %.