Newsletter
3/2022
Using unavoidable CO₂ emissions as feedstock for numerous products
CCU technologies and applications are gaining momentum within the cement industry
The abatement of CO₂ emissions from industry processes is recognised as a key challenge for achieving carbon neutrality in line with the objectives of the EU Green Deal to be achieved by 2050. With regard to CO₂ reduction in the clinker production process, it is now widely acknowledged that the abatement of process-related CO₂ emissions will require the capturing and sequestration or utilisation of CO₂ from cement plants. Through its academic chair at the University of Mons, ECRA has been investigating opportunities for carbon capture and utilisation in the cement industry. ECRA’s network now serves as a basis for further deployment and cooperation.
The target of carbon capture and utilisation is to separate CO₂ from the flue gas to produce new valuable products. Various technologies which are capable of capturing CO₂ from cement flue gases have been developed in the past years. Now the industry needs to find applications with a high demand for the captured CO₂.
Scaling up carbon capture technologies
With different types of integrated technologies (such as Oxyfuel, Indirect Calcination or Ca-Looping) and a broad spectrum of post-combustion solutions (for example amine technology), capture technologies can be adjusted to fit the respective site-specific conditions and requirements. Developing a site-specific CCUS strategy is complex, due to various factors like the availability of renewable energy having to be taken into account. Especially those cement plant locations offering no direct access to a CO₂ transport system may require a strategy which includes the utilisation of CO₂.
Production of e-fuels, chemicals and syngas
The conversion of CO₂ to several other molecules offers the greatest possibilities for circular value chains. The potential of synthetic fuels for those transport sectors, where e-mobility is limited (for example, sea transport and air traffic), is high. Basically, electrochemical or catalytic processes are not limited to one type of CO₂ product. Nevertheless, only a few projects and topics have been developed to TRL 6 or higher. The Fischer-Tropsch synthesis (FTS) for production of synthetic fuels offers a huge potential as it has been a well-proven technology for many years. In particular, the direct conversion of CO₂ to methane, methanol and longer hydrocarbons unlocks access to several follow-up fields of application. Sunfire’s breakthrough development in a Kopernikus project produces H₂ and CO from CO₂ and water in one Co-Electrolysis. This dramatically increases efficiency and decreases effort and costs. The produced Syngas (a mixture of H₂ and CO) is used by Ineratec technology (Fig. 1) in the FTS to produce a mixture of hydrocarbons which can then be hydrocracked to desired synthetic fuels.
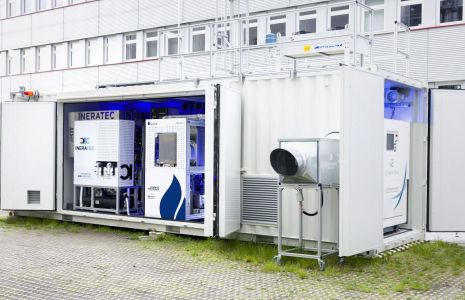
Figure 1: Modular reactor system by Ineratec for syngas production © Sunfire GmbH
Polycarbonates and polyurethanes can be produced by CO and CO₂ from gases from metallurgical processes as proven by Carbon2Polymers, a sub-project of Carbon2Chem from the German steel industry. Since polymerisation reactions tend to be sensitive to impurities, the gas purification process has a special meaning in this context. With every new product application, such as mattresses made from Cardyon®, the circular economy comes closer one step at a time, offering new potentials for the cement industry as CO₂ customers. This utilisation path is gaining importance in the cement industry due to its high demand for CO₂. Various projects, such as Westküste100, Vicat’s Montalieu project, C2PAT or catch4climate are preparing the ground for commercial applications.
Direct use of CO₂
Among others, the ECCO2 joint venture plans to use the captured and treated CO₂ in a process known as carbon fertilisation in regional greenhouses. This process is known to improve crop productivity by enhancing natural photosynthesis. At commissioning, the project is planned to use 10% of the cement plants CO₂ emissions and will thereby fulfil an important milestone in 2023. Using the gas to feed microalgae which then can be fed to fish is the concept behind HeidelbergCement subsidiary Ciments du Maroc (Fig. 2).
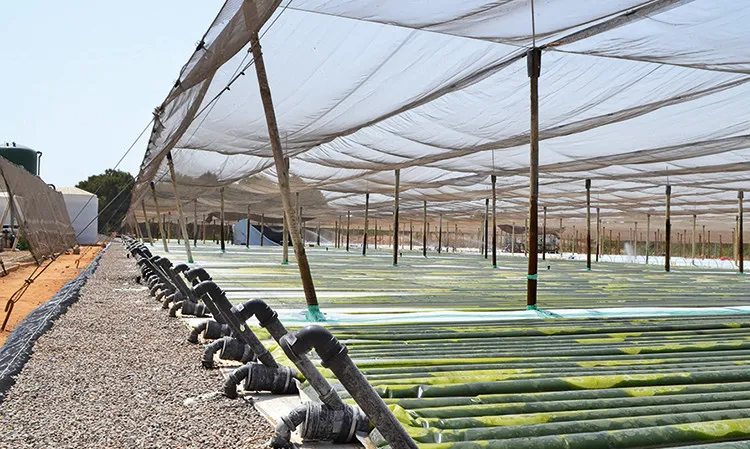
Figure 2: Microalgae project using CO₂ from a nearby cement plant flue gas stream to produce fish feed © HeidelbergCement AG/gettyimages
Mineral carbonation
The possibility to absorb CO₂ in hardened cement paste, to use CO₂ in the production of fresh concrete (CarbonCure) or to mineralise crushed concrete (C₂inCO₂, Fast-Carb, Neustark) or mineral wastes (Carbon8) is of special interest for the decarbonisation of cement and concrete. Those projects combine capture and utilisation and currently have the possibility to reduce the CO₂ footprint of cement by up to 20 kg per produced tonne. Research is being undertaken to improve the kinetics and the energy demand (see here).
Individual site-adjusted CCU strategies
Each of the mentioned pathways and several more to put CO₂ to good use will grow in importance in the future. Creating an actual value instead of costs for emission certificates may open up promising market fields. Amongst other aspects, the availability of renewable energy, necessary materials and the proximity to other industrial clusters or users will influence the decision tree regarding which CCU application fits best to each specific location.