NEWSLETTER
2/2024
Fuels and kiln technology of the future
The impact of novel technologies to reduce carbon emissions
New technologies are set to play a crucial role in the future of clinker production. Innovations such as CO₂ capture using solid sorbents, cryogenic solutions, hydrogen combustion, and electrical heating are currently under investigation or have already been tested at the pilot scale. These advancements are expected to have a significant impact on kiln technology, altering burner designs, and leading to major changes in operational practices. As these technologies evolve, they are likely to shape the future landscape of cement production, driving greater efficiency and sustainability.
Carbon Capture
Carbon capture technologies prevent CO₂ from entering the atmosphere by separating it from the process flue gases and purifying it to the level required for sequestration or utilisation. Several CO₂ capture technologies have been developed in recent years: post-combustion technologies as well as integrated processes. For selecting an appropriate capture method for a plant, its site-specific constraints (plant location, available materials, available space, bottlenecks to retrofitting) form a complex decision tree. The application of carbon capture to cement plants changes the standard way of operating the clinker burning process as not only cement clinker but also CO₂ becomes a product that must meet certain product criteria. In order to guarantee the required purity of CO₂ and to achieve the lowest possible energy input, it is necessary to stabilise the kiln operation, reduce the number of shutdowns and qualify the flue gas composition. Consequently, the selection of an appropriate fuel source becomes a crucial element in the operation of carbon capture installations.
In addition, integrated capture technologies will change the production process. For instance, the Oxyfuel technology can be implemented in different designs, based on the same basic principle of oxygen combustion, but with different levels of integration. Due to the removal of nitrogen, the combustion atmosphere in the kiln is dominated by O₂ and CO₂. Replacing conventional ambient air with oxygen results in a CO₂ enrichment of up to 80 - 90% by volume on a dry basis. The achievable CO₂ concentration in the dis-charged flue gas is highly dependent on the amount of false air entering the system. A CO₂ Processing Unit purifies the CO₂ to the desired final specification. The Oxyfuel process differs from conventional operation in a number of important respects. This applies in particular to its energy balance and the relationship between the enthalpy flow of the kiln gas and the energy required for the chemical/mineralogical reactions of the kiln feed. In addition to the optimum temperature profile for clinker phase formation, the optimum oxygen content depends to a large extent on the design of the kiln plant and therefore on the implementation option: retrofit or new installation.
Hydrogen combustion
The use of hydrogen gas alongside alternative fuels (AF) offers significant potential to reduce CO₂ emissions in the cement industry. Unlike conventional fuels, hydrogen combustion produces only water (H₂O), with no direct CO₂ emissions.
Another advantage is the high efficiency of hydrogen use in cement production, as it does not require energy-intensive compression, as is the case in other industries. The main challenge is to ensure a sufficient supply of carbon-neutral electricity to produce hydrogen possibly at plant site.
In 2022, the largest known kiln test using hydrogen was conducted in the UK as part of the Fuel Switch project, supported by the Department for Business, Energy and Industrial Strategy (BEIS) and the Mineral Products Association. This test successfully operated a cement kiln with a net zero carbon fuel mix at the primary burner, demonstrating the potential of hydrogen in achieving carbon-neutral cement production (Fig. 1).
Electrical heating
Electric processes have potential for clinker production, but they face significant challenges. Most methods have only been tested on a small scale and are often batch processes, in contrast to the continuous rotary kiln. Technologies such as microwave furnaces, electron beams, and electric arc furnaces each have drawbacks such as energy loss, uneven heating or reducing atmospheres. Plasma torches or resistance heating may offer solutions for specific steps, but their compatibility with the overall process needs to be tested (Fig. 2).
A key challenge is to scale up these methods to industrial levels and to ensure sufficient renewable electricity. For example, a plant producing 3,000 tonnes of clinker per day would require at least 120 MW of electrical power. Despite the challenges, electrical clinker production could allow for alternative raw materials and lower CO₂ emissions, making it a promising area for further research.
Learn more about ECRA's new online seminar "Fuels of the Future" on 10 October 2024
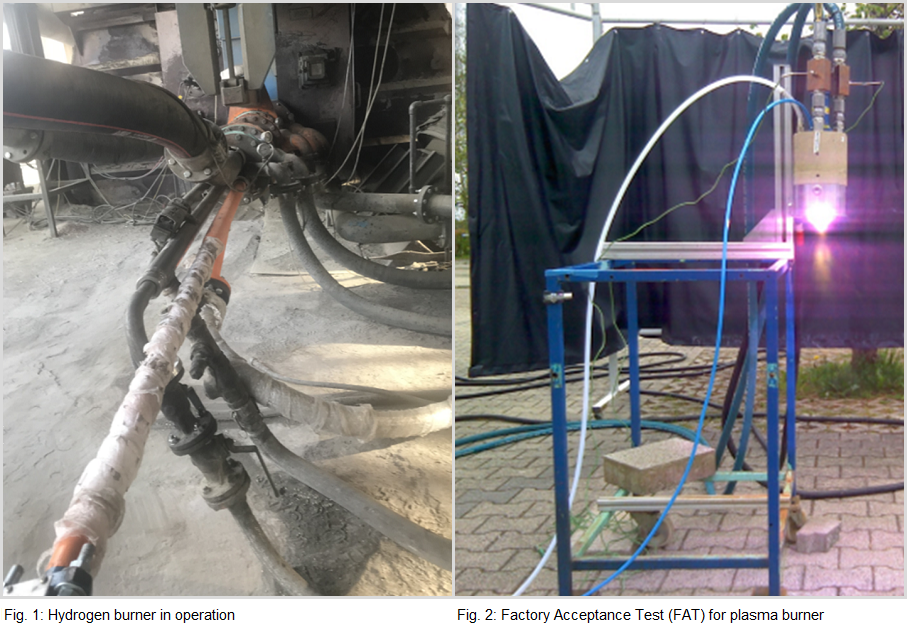