Newsletter
4/2021
Sulphur and chloride cycles and the use of alternative fuels or raw materials
High removal efficiency for bypasses in individual kiln situations
Raw materials and fuels for cement production contain certain portions of volatiles such as chloride, sulphur and alkalis. In the past decade, the increased use of alternative fuels and alternative raw materials has led to higher inputs of these compounds at many rotary cement kilns. These tend to be enriched through circulation between the sintering zone of the kiln and the lowermost cyclone stage of the preheater. This leads to a higher potential for coating formation in the meal duct to the kiln inlet, as well as coating and ring build-ups in the rotary kiln. For smooth operation it is important to limit these cycles and, if necessary, reduce them. Cement kilns are therefore increasingly equipped with bypass systems.
Modern plants for burning cement clinker operate according to the counter-current principle. This means that the prepared raw meal is preheated by the hot kiln exhaust gas. At the same time, hot clinker from the kiln is used to preheat the combustion air. Under these condtions, chloride, sulphur, and alkali compounds evaporate in the sintering zone and condensate in the lower part of the preheater. Depending on the specific situation, these compounds can build up cycles between the rotary kiln and the preheater which can affect the kiln operation.
Options to limit cycles
To ensure trouble-free kiln operation, sulphur and chloride cycles can be limited in two ways: either by reducing the input of these compounds, or by removing part of the circulating materials from the kiln preheater system. Such a removal is most efficient at the point of highest concentration when the loss of material, gas and thermal energy is at its lowest. However, in order to achieve this, the circulation profile of the whole kiln system must be known and has to be determined by measurements.
In kilns with cyclone preheaters three options have been proven to limit the inner cycles:
- At lower circulation levels, dust can be removed from the exhaust gas dust filter, preferably at times when the raw mill is not in operation.
- The installation of a meal bypass system can also be used for the purpose of the removal of less volatile materials. In this case hot meal can be removed from a lower cyclone stage.
- Finally, the installation of a gas bypass has proved to be particularly effective for the limitation of chloride cycles. With low amounts, the discharged material from the process can be bypassed beside the clinker burning process and used as an additional component in the cement. Large amounts and highly contaminated material have to be recovered in other ways or deposited.
Design of gas bypass systems
Gas bypass systems should effectively remove the largely evaporated alkali chlorides at the prevailing temperatures in the kiln inlet and riser duct with low kiln feed losses. Therefore, the alkali chloride removal is most efficient in those parts of the riser duct where dust concentrations are low and gas temperatures are high. However, because alkali sulphates are already combined with particles to a large extent in this part of the kiln, they tend to remain in the kiln system because of the low-dust takeout. As a consequence, gas bypass systems have to be dimensioned according to the input of alkalis, sulphates and chlorides, their molar ratio, and also the lime saturation factor of the raw material and the temperature profile in the kiln plant. Figure 1 schematically shows the kiln inlet area of a cyclone preheater with a modern gas bypass system.
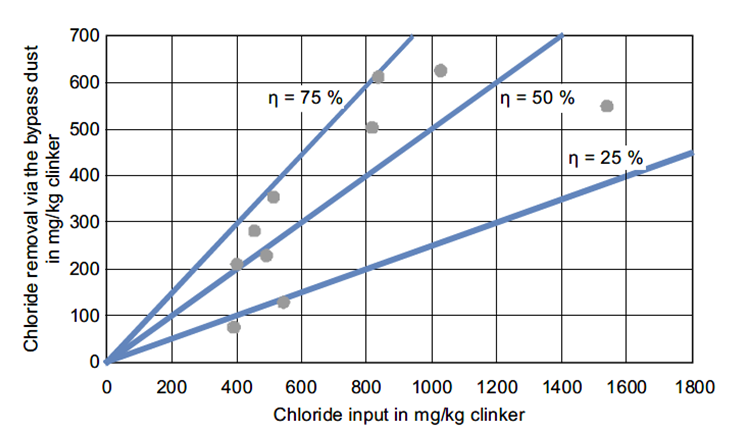
Figure 1: Chloride-removing efficiency of bypass systems in various works
The most efficient point for removing chloride from the system is the kiln inlet chamber or the lower part of the riser duct, where the chloride concentration in the kiln flue gas is highest. To minimise the loss of kiln feed, the takeoff of the bypass gas should be located at a point where the flue gas carries a minimum of kiln dust. CFD modelling helps to describe the flow pattern of the flue gas, and to evaluate the point where the bypass gas takeout should be located.
Chlorine and Sulphate removal at bypass systems
Figures 1 and 2 show the efficiency of bypass systems at various kiln lines for the removal of chloride and sulphate, respectively. The investigations have shown that the efficiencies of bypasses are between 20 and 75 % for chlorides with reference to the total input of chlorides into the kiln system. The removal rates for sulphur can be adjusted to be between 2 and 12 % with reference to the input of sulphur.
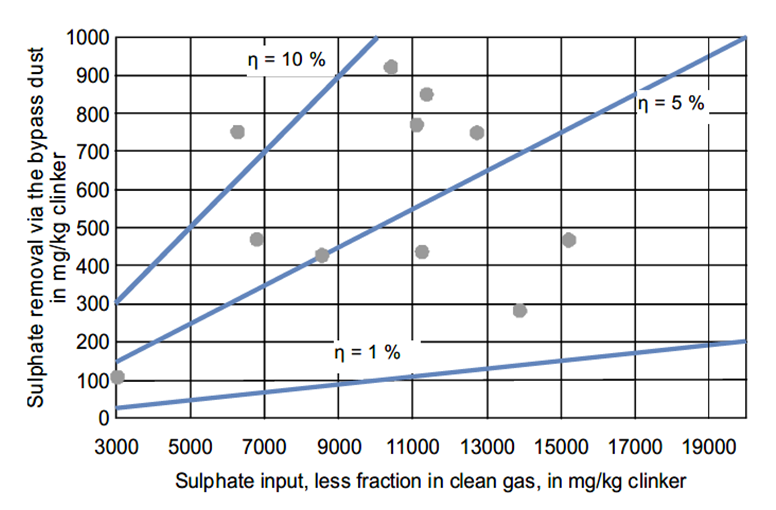
Figure 2: Sulphate-removing efficiency of bypass systems
Gas bypass systems are highly efficient in removing chloride from the system, but merely moderately efficient for sulphate and alkalis. A hot meal bypass is capable of taking off sulphate or alkalis due to the discharge point (Figure 3).
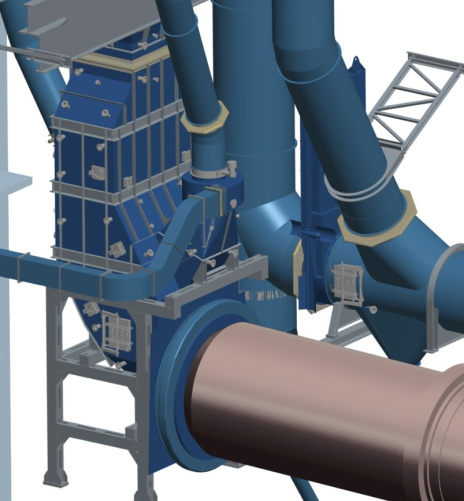
Figure 3: Modern cyclone preheater with a gas bypass
The removal of bypass gas is linked to the precipitation of considerable masses of bypass dust. Besides partly carbonated and partly decarbonated hot meal, the dust contains alkali chlorides and sulphur compounds as well as intermediate products such as C2S and CA. The utilisation of bypass dust depends on the composition of the dust. The biggest portion of the bypass dust is used as a minor additional constituent in cement, other possibilities are its use as construction material in different applications.